100% Original Factory Screw Roller Conveyor to Belarus Factory
100% Original Factory Screw Roller Conveyor to Belarus Factory Detail:
Hairise roller conveyors are a cost effective way for moving boxes and pallets. We offer custom designs. Select the drive concept (gravity, tangential chain, or motorized roller) that is optimal for your application. All systems are available as straights and curves. A broad assortment of roller types ensures a roller conveyor concept adapted to your requirements.
Dimensions – Technical Data
- Conveyor width W: 500 and 1000mm
- Conveyor length: Custom
- Roller Power: Motorized or Nonmotorized
- Roller Thickess:1.2mm-2mm
- Roller Material: SS, Carbon Steel
- Drive & speed: to v = 30 m/min
- Drive version: AC
Product detail pictures:
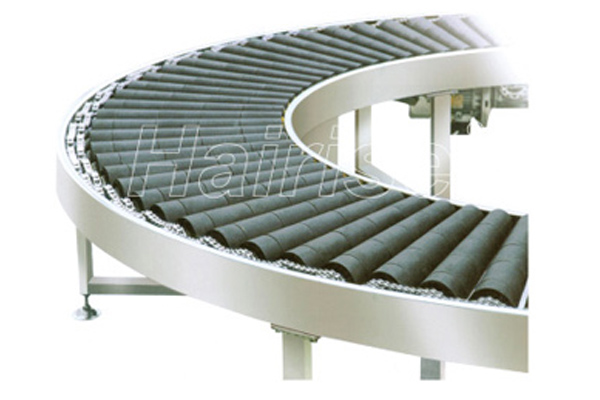
Our primary objective will be to offer you our shoppers a serious and responsible enterprise relationship, supplying personalized attention to all of them for 100% Original Factory Screw Roller Conveyor to Belarus Factory, The product will supply to all over the world, such as: Lesotho, Anguilla, Doha, Genuinely should really any of those objects be of interest to you, please let us know. We'll be pleased to present you a quotation on receipt of one's detailed specifications. We have our personal professional R&D enginners to meet any with the requriements, We look forward to receiving your enquires soon and hope to have the chance to work together with you inside the future. Welcome to take a look at our organization.
This custom conveyor system was retro-fitted to a vibratory feeder bowl to accommodate a part change that required a secondary inspection operation. The system consisted of a pair of Auto-Kinetics belt conveyors with custom tooling to maintain part orientation, and a 3-position shuttle mechanism between the conveyors.
Parts exiting the vibratory bowl fed into the first conveyor. An escapement metered a single part into the shuttle while in the left position, where a camera inspected the part for the proper seating of an internal washer. If the part was bad, the shuttle cycled to the center position and a pneumatic cylinder pushed the part out of the shuttle into a catch bin. If the part was good, the shuttle cycled to the right position, where a second pneumatic cylinder pushed the part onto the second conveyor, which fed into the customer’s automatic assembly operation.
The system included photoelectric sensors to detect full conveyors, a photoelectric sensor to detect a part in place in the shuttle mechanism, proximity sensors to detect the shuttle in each position, and sensors on the escapement to detect its position. All sensor and valve cables were wired into a junction box for the customer to interface with their control system.

We have been looking for a professional and responsible supplier, and now we find it.
