Big Discount Har P712 Light Power Connector Type Conveyor Parts to Albania Manufacturers
Big Discount Har P712 Light Power Connector Type Conveyor Parts to Albania Manufacturers Detail:
Product detail pictures:
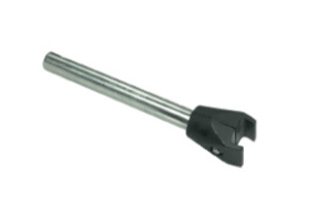
Our firm sticks towards the basic principle of "Quality could be the life of your organization, and name may be the soul of it" for Big Discount Har P712 Light Power Connector Type Conveyor Parts to Albania Manufacturers, The product will supply to all over the world, such as: Manila, Albania, Laos, Insisting over the high-quality generation line management and prospects guide provider, we've made our resolution to supply our shoppers using the initially stage purchasing and soon after provider working experience. Preserving the prevailing helpful relations with our prospects, we even now innovate our product lists the many time to meet up with the brand new wants and stick to the latest trend of this business in Ahmedabad. We're ready to facial area the difficulties and make the transform to grasp many of the possibilities in international trade.
16′ x 30″ Incline Conveyor

The factory can meet continuously developing economic and market needs, so that their products are widely recognized and trusted, and that's why we chose this company.
