China Manufacturer for Modular Belts P=1.73″ Belt Har 6200NP flush grid Supply to Malawi
China Manufacturer for Modular Belts P=1.73″ Belt Har 6200NP flush grid Supply to Malawi Detail:
Har 6200NP flush grid
Thickness: 18mm
Opening area: 20%
It is easy to clean and can resist heat because of good plastic rubber material. So our products have some advantages, for example,
1. Easy installation and maintenance
2. High mechanical strength and wear resistance
3. Low friction coefficient
4. Excellent product handling
5. High performance
We are a leading manufacturer of modular belts with professional team; we can provide you with excellent quality items. This kind of modular belt can be used in the following industries:
Beverage industry such as acceleration, depletive and accumulation.
Food industry such as cool off lines and pack lines.
Meat industry such as tray pack line and metal detectors.
It is mainly used in food, soft drink, packaging & manufacturing, tobacco, medicine & chemical, electronics, automobiles and logistics industries. It is also used in Meat poultry applications including packaging lines, Can making/filling lines and accumulation tables.
Product detail pictures:
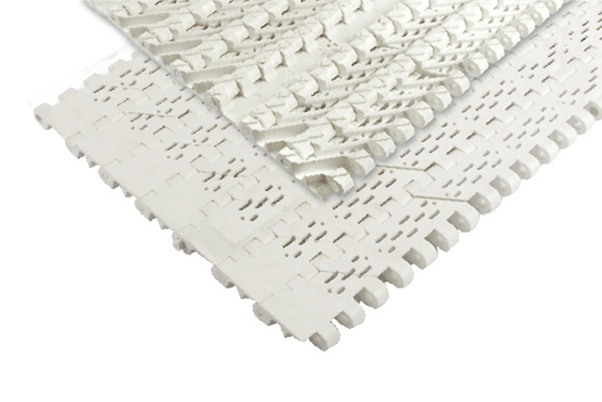
Like a result of ours specialty and repair consciousness, our enterprise has won a superb popularity amid buyers everywhere in the environment for China Manufacturer for Modular Belts P=1.73″ Belt Har 6200NP flush grid Supply to Malawi, The product will supply to all over the world, such as: Indonesia, Falkland Islands (Malvinas), Algeria, We hope we can establish long-term cooperation with all of the customers, and hope we can improve competitiveness and achieve the win-win situation together with the customers. We sincerely welcome the customers from all over the world to contact us for anything you have to have!Welcome all customers both at home and abroad to visit our factory. We hope to have win-win business relationships with you, and create a better tomorrow.
PRF – PLASTICS RECYCLING FACILITIES
www.amutecotech.it
AMUT plant is able to cover the comprehensive recycling flow from mixed plastics sorting up to the delivery of flakes. These flakes have a quality level suitable to be re-used in further extrusion, injection or thermoforming process.
The plant reclaims polyolefin thermoplastics scraps to be transformed into granules with an output of 10 Tons/h.
The thermoplastic scraps come from the urban and industrial separate collection and they are previously selected as:
- HDPE / PP containers and bottles for foods.
- HDPE / PP containers and bottles for detergents and chemicals.
Plastics at inlet: HDPE and PP (75%), heavy plastics (25%).
The plant is fed by mixed plastics materials packed into bales, loaded by a forklift on the extracting chain conveyor installed in a pit, weighing system equipped with, and then conveyed to the “bales breaker machine”, properly designed and manufactured to break up bales mainly composed by plastic materials. This machine doesn’t shred material but gets back bulk material in order to feed the recovery plant in a constant and regular way.
Breaking up of the bales is assured by the circular motion of a drum equipped with fix teeth. The rotor’s sharp tools enter the bales separating in this way all materials that fall in the below conveyor belt, conveying materials to the pre-sorting picking cabin where pickers take way bulky materials, mainly represented by cardboard and film, from the stream. After this first selection, by a feeding conveyor, the material flow is conveyed in the rotary trommel, where the separation depends on size. Three different streams are possible.
1. Material having size smaller than 30 mm falls on a conveyor belt, where is conveyed, jointly to the one fine coming from the ballistic separators, to the residue storing unit.
2. Material having size between 30 and 260 mm, is conveyed to the ballistic separator where the rolling shape and the hard materials are separated from the light and flat ones by the paddles sussultory movement. Furthermore, thanks to the grids installed on the paddles, fine material not yet separated by the rotary trommel, is evacuated and conveyed to the special storing unit. Flat and light material are conveyed upward by a conveyor.
“Rolling shape and hard materials” sorted by the action of the ballistic separator, are conveyed to the plastics automatic selection line where plastic material will be automatically selected by optical readers.
3. Oversize materials stream, having size bigger than 260 mm is conveyed to the bulky materials picking line, where, different types of materials, mainly film and good plastics to be sent to the automatic line are manually selected and discharged in chutes.
In order to get the higher quality of materials, after the NIR optical reader they are provided QC (quality control) stations, where pickers recycle errors, conveyed at the beginning of the automatic line to get more efficient the line. A manual checking line is also provided.
Before entering the automatic line, “rolling shape and hard material” (plastic materials stream) stream passes through a de-metallization line, consisting of an over band magnetic separator used for ferrous materials and, an Eddy Current System (based on the Foucaults currents principle), used for no-ferrous metals. Ferrous and no-ferrous materials selected in the de-metallization line, are weighed by weighing system hopper and then discharged into hook-lift containers.

The factory workers have rich industry knowledge and operational experience, we learned a lot in working with them,we are extremely grateful that we can encount a good company has excellent wokers.
