New Delivery for Carbon Steel Single-Chain Tapered Roller for Grenada Factories
New Delivery for Carbon Steel Single-Chain Tapered Roller for Grenada Factories Detail:
Product detail pictures:
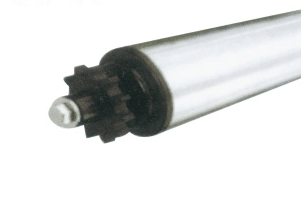
Our business aims to operating faithfully, serving to all of our buyers , and working in new technology and new machine continuously for New Delivery for Carbon Steel Single-Chain Tapered Roller for Grenada Factories, The product will supply to all over the world, such as: Azerbaijan, Mozambique, Houston, With the support of our highly experienced professionals, we manufacture and supply best quality items. These are quality tested at various occasions to ensure only flawless range is delivered to customers, we also customize the array as per the require of customers to meet the requirement of customers.
This project involved the design and fabrication of a sauce-dosing conveyor system. The machine is designed to advance four trays per index. When the index stops, fiber optic detectors determine whether a tray is present underneath the dosing nozzle. If a tray(s) is missing, then that nozzle does not open. The PLC and HMI is recipe-driven, so for a given product, the number of dosing strokes can be different. The weight of sauce per tray is determined by the stroke length of the piston filler; the longer the stroke the greater the weight. The hopper is equipped with a stir paddle and detection probe. As sauce is expended, a pressurized filling tank automatically refills the hopper.
I used an Allen-Bradley MicroLogix 1400 PLC and AVG HMI. A PowerFlex 40P and a Marathon vector motor indexes the conveyor. I used step-logic and encoder feedback to control the index. A second PowerFlex 40 controls the speed of a radius discharge conveyor. Trays leaving the sauce conveyor are ejected onto the radius conveyor and into a vacuum packaging machine.
All welding for this project was performed using the gas tungsten arc welding (GTAW) process, in accordance with AWS D9.1M/D9.1; D1.6/1.6M; and D18.1/18.1M. There were a number of areas that required autogenous welding, such as the injector nozzles. All tubing was welded in accordance with D18.1/18.1M, in order to prevent oxidation (sugaring) of the surfaces exposed to product.
The PLC and HMI have a very sophisticated application program. I included a number of service and maintenance screens, whereby the VFD operating parameters can be monitored (via RS485); for example, DC bus voltage, output voltage, output current, output frequency, etc. In addition, the VFD can be tuned from HMI.
The index speed, length, doses/tray, discharge speed, and other parameters can be changed for a given recipe selection. The HMI is equipped with an audible alert and popup messages appear automatically, to warn of any system problems (e.g., loss of air pressure, failure in the downstream packaging machine, etc.). If the downstream equipment faults, then the dosing conveyor automatically executes a cycle stop.

The supplier cooperation attitude is very good, encountered various problems, always willing to cooperate with us, to us as the real God.
